Ultrasonic welding has become an essential joining process in many high-tech and high-volume manufacturing environments. Known for its speed, precision, and ability to bond materials without adhesives or fasteners, ultrasonic welding is used extensively in industries where quality and efficiency are paramount. At our US automated machine manufacturing company, we design ultrasonic welding systems that meet the unique demands of several key sectors.
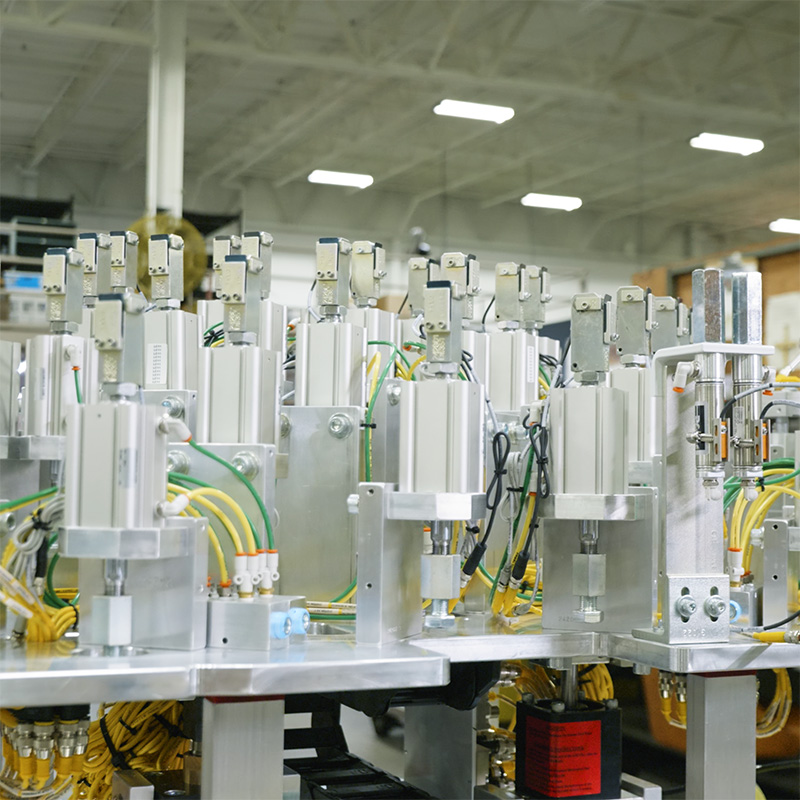
Automotive Industry
Ultrasonic welding plays a major role in modern automotive manufacturing. From assembling interior components like dashboards and door panels to bonding under-the-hood parts such as wiring harnesses and sensors, this method ensures strong, clean, and consistent joins.
The non-invasive nature of ultrasonic welding also makes it ideal for joining thermoplastics and lightweight composite materials used in electric vehicle (EV) production.
Furniture and Seating Manufacturing
In the furniture sector, especially for modular and ergonomic seating, ultrasonic welding is used to join foam-backed fabrics, nonwoven materials, and plastic components. The process enables sleek, seamless finishes without the need for visible stitching or glue.
This not only enhances the aesthetics of the final product but also improves production speed and durability—particularly in office and automotive seating applications.
Packaging Industry
is widely adopted in the packaging industry for sealing blister packs, clamshells, tubes, and flexible films. Unlike traditional heat sealing, ultrasonic welding creates strong bonds without deforming or overheating the material.
It’s especially valuable for food-safe and tamper-evident packaging where precision, speed, and cleanliness are critical. Automation-ready ultrasonic sealers help manufacturers meet high-volume demands with consistent results.
Electronics and Electrical Applications
For electronics manufacturing,
offers a reliable solution for joining delicate components without introducing thermal damage. It’s used for welding wire harnesses, battery tabs, sensors, and circuit protection devices.Since it doesn’t require solder or adhesives, ultrasonic welding helps ensure optimal conductivity, mechanical strength, and quality assurance in high-performance electronic assemblies.
Medical Device Manufacturing
In the medical field, ultrasonic welding supports the assembly of products like IV catheters, filters, valves, and surgical instruments. It allows for precise, repeatable welds that maintain the integrity of delicate plastics and meet strict hygiene standards. Since no solvents or adhesives are used, the process is well-suited for producing sterile, single-use medical items efficiently and safely.
New Energy Technologies
Ultrasonic welding is increasingly vital in the production of new energy solutions, especially lithium-ion batteries and fuel cell components. This technique enables the joining of copper and aluminum tabs with high precision and minimal heat generation—preserving the structural integrity of critical battery parts. It supports growing demand in the electric vehicle and renewable energy markets.